Work Page 4-25
Early 1900s 5 string
38 bracket - 11" Spun-over rim
John Stratton of NYC is listed as a maker or distributor of Monarch brand banjos. It is questionable if he actually manufactured banjos. He likely contracted them with established manufacturer's.
He died around 1912.
Some say that Buckabee may have been the actual maker.
Mail order banjos are harder to I.D. with no Maker names or serial numbers.
Some of us Luthiers refer to these as the "bracket war" days, when builders were attempting to find ways to keep hide heads tight when it was humid.
38 is the most I have had to work with on an 11" rim.
He died around 1912.
Some say that Buckabee may have been the actual maker.
Mail order banjos are harder to I.D. with no Maker names or serial numbers.
Some of us Luthiers refer to these as the "bracket war" days, when builders were attempting to find ways to keep hide heads tight when it was humid.
38 is the most I have had to work with on an 11" rim.
Clean- repair as needed to make playable
Instrument in fair condition, all original hardware
Mahogany, Metal inlay, one missing.
Violin style pegs
Wooden tailpiece
Brass "Monarch" plate is actually a slide over cover positioned resembles what now we would call a "frailing scoop"
A lowered area so that certain types of picking styles can be implemented.
My friend told me it was done by Stratton just as a logo and that it was a common fixture on Buckabee's.
But it would still work as a scoop.
Previous dowel reset (installed upside down)
Dowel needs to be heated and pulled.
*********
Heel is cracked, either from this procedure or the head being cranked too far down.
I did not even see that when we were going over this. *(Gettin' old)
It is a weird grain pattern and it is mahogany very dry after over 100 years
I will repair it when I pulled the dowel and it will be ok.
Decent frets on a fairly level fingerboard, a good sign.
Instrument in fair condition, all original hardware
Mahogany, Metal inlay, one missing.
Violin style pegs
Wooden tailpiece
Brass "Monarch" plate is actually a slide over cover positioned resembles what now we would call a "frailing scoop"
A lowered area so that certain types of picking styles can be implemented.
My friend told me it was done by Stratton just as a logo and that it was a common fixture on Buckabee's.
But it would still work as a scoop.
Previous dowel reset (installed upside down)
Dowel needs to be heated and pulled.
*********
Heel is cracked, either from this procedure or the head being cranked too far down.
I did not even see that when we were going over this. *(Gettin' old)
It is a weird grain pattern and it is mahogany very dry after over 100 years
I will repair it when I pulled the dowel and it will be ok.
Decent frets on a fairly level fingerboard, a good sign.
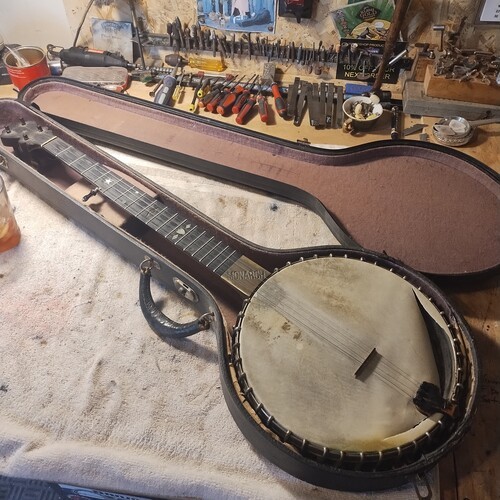
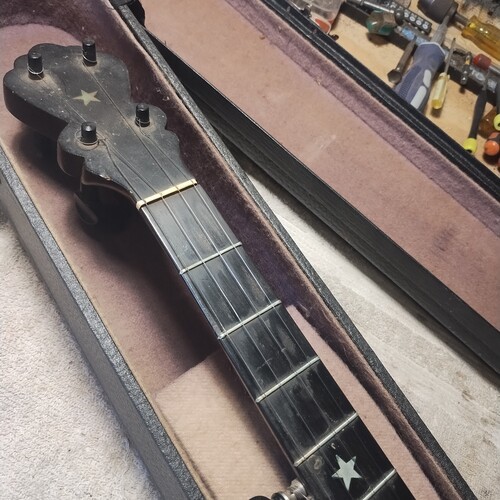
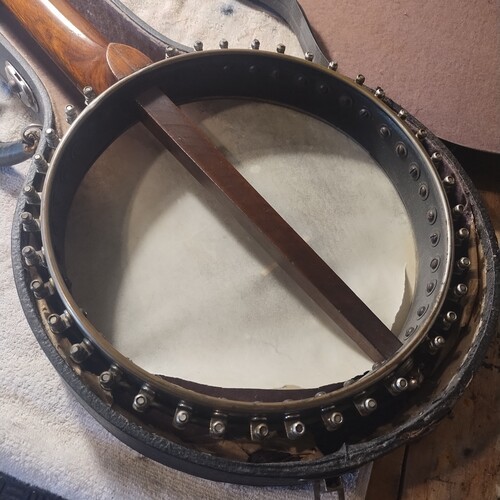
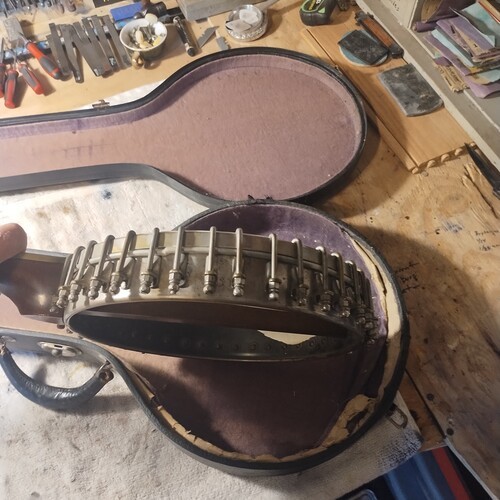
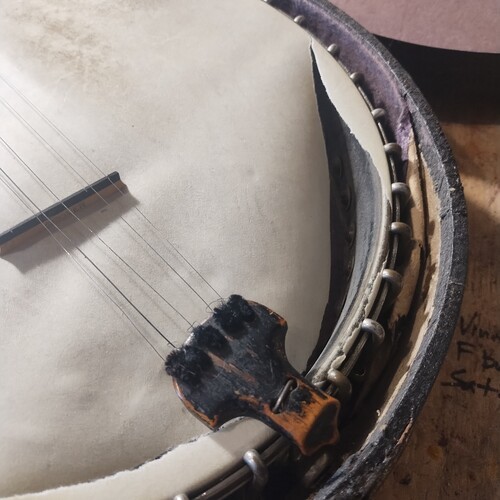
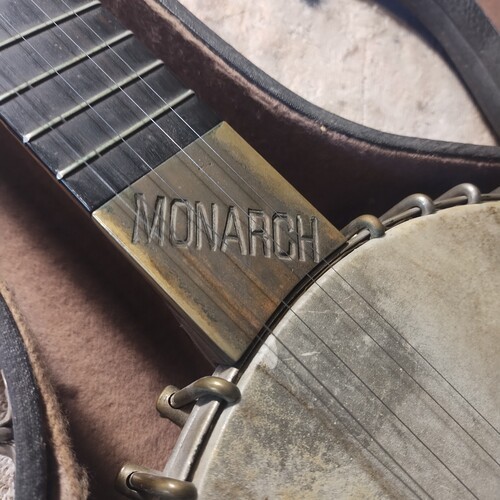
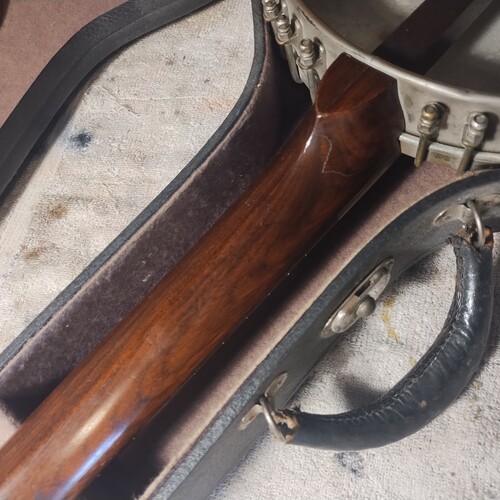
The pic where I saw the heel crack.
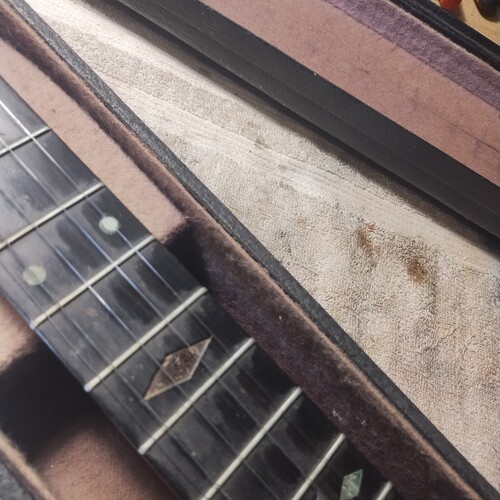
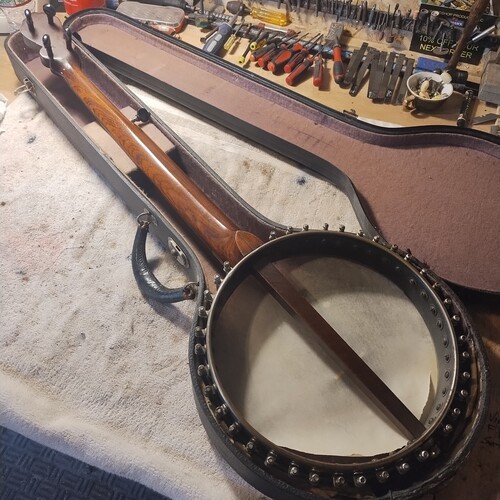
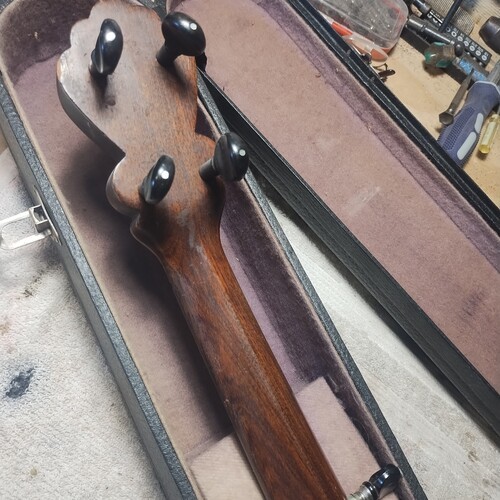
Repair Sequence
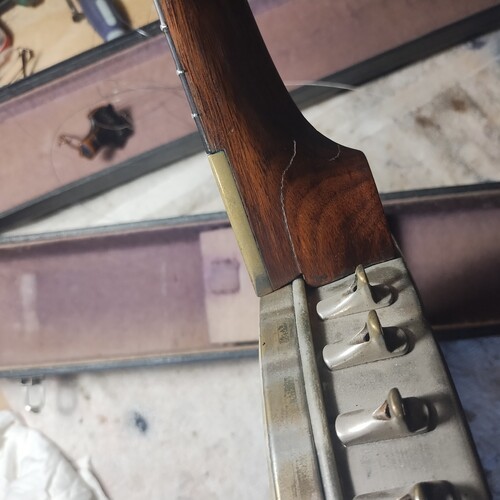
A lot of grain for a heel.
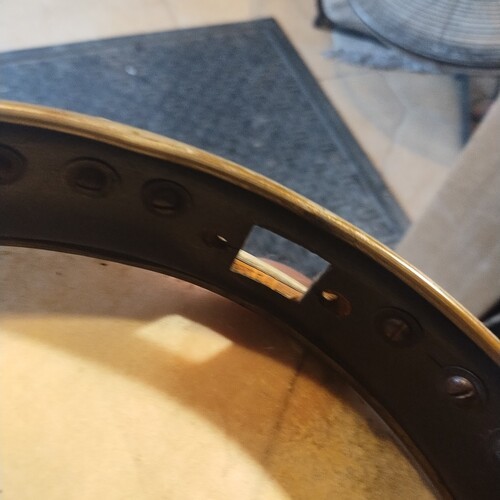
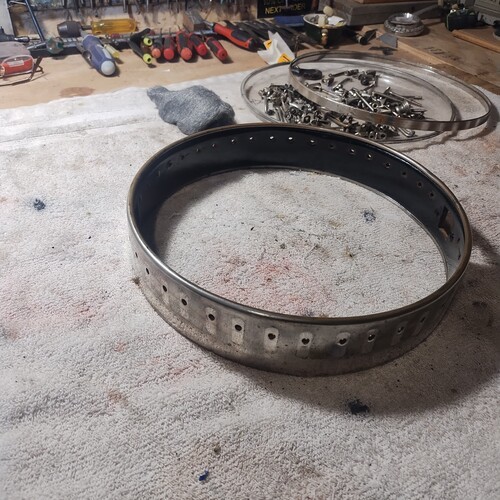
Nickel oxidized, some brassing and pitting, normal.
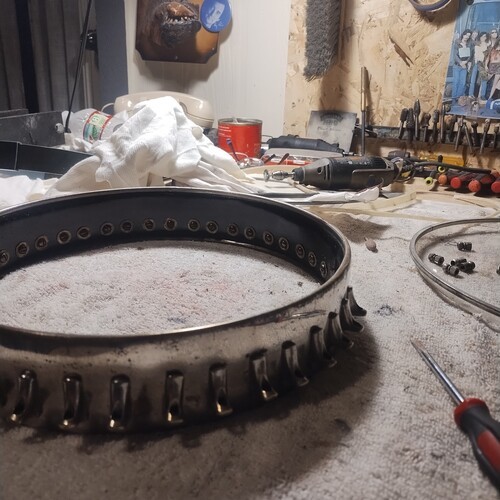

Ready for neck work
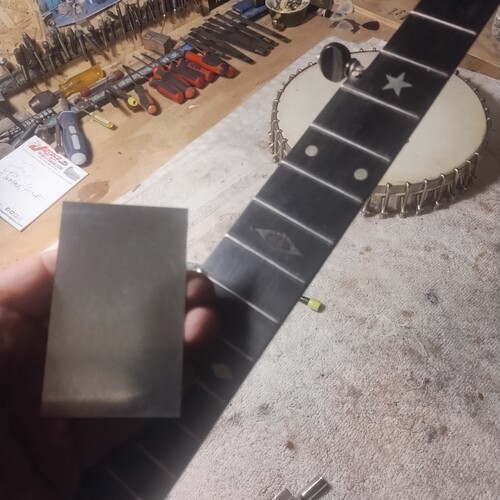
Aluminum sheet, to make n inlay.
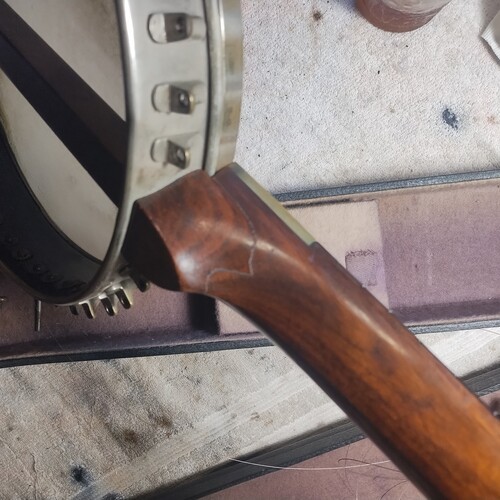
You can see the head maxed out against it
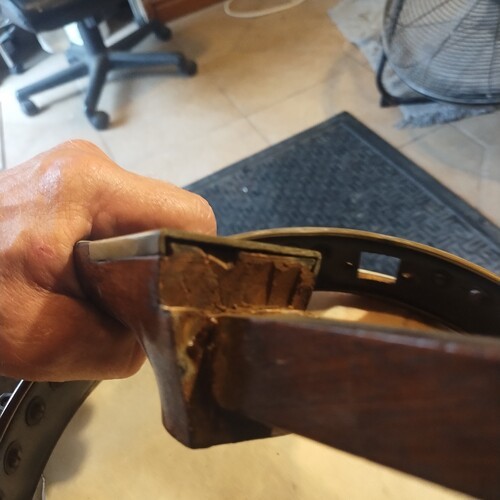
They used to screw into the neck here, bad design.
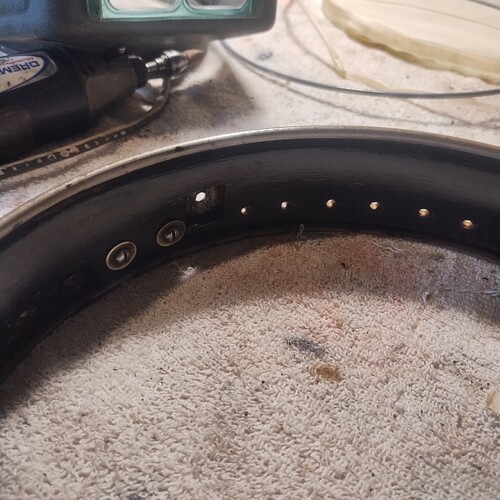
Inside wood re-coated with clear, hardware cleened
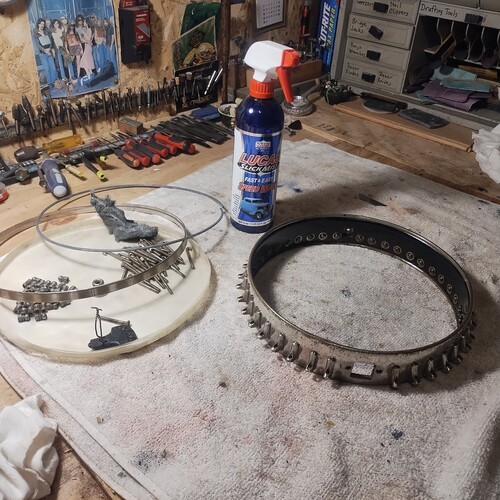
Ready for head
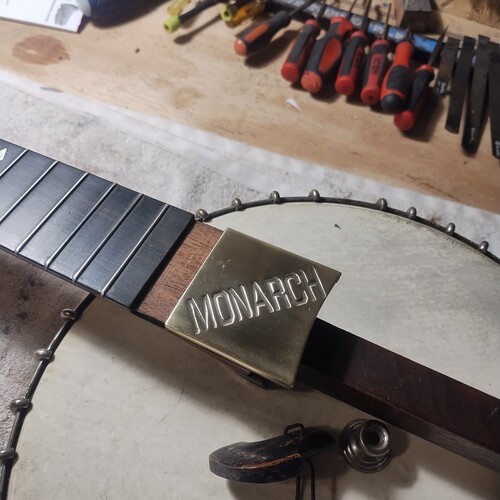
Showing the slide
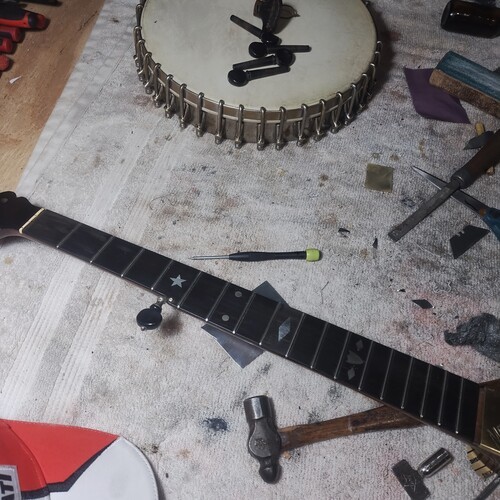
Inlay Installed
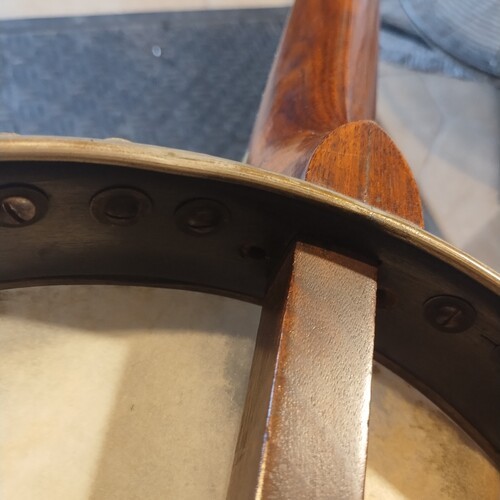
Heel cap crack probably due to dowel reset. Inside rim attaching screws missing.
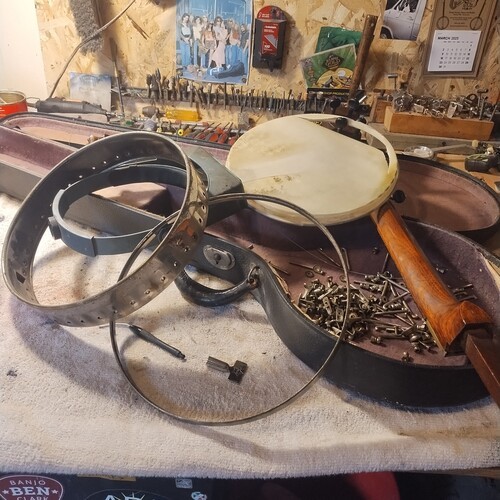
Ready to clean
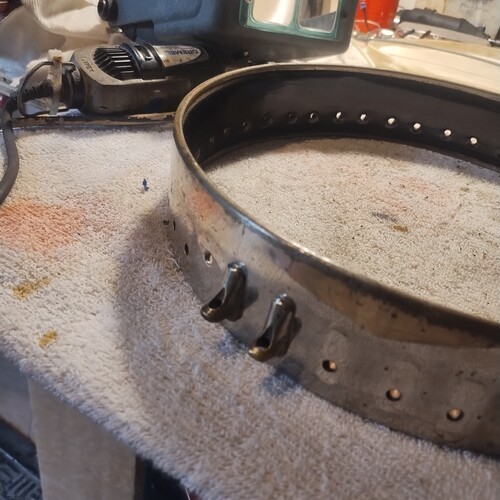
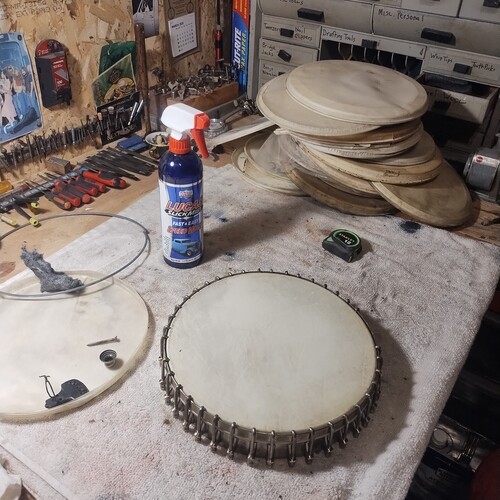
Found a vintage hide to re-purpose.
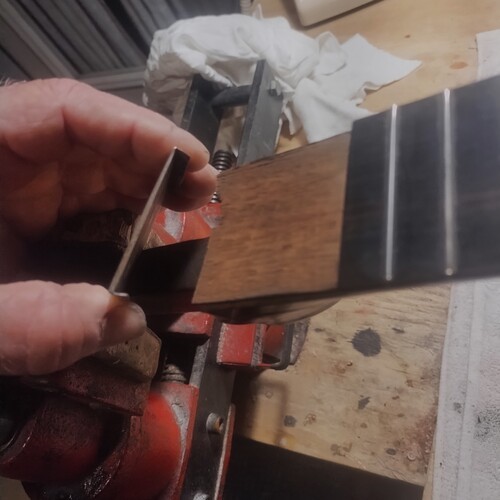
Some wood is chipped underside, will repair.
NECK WORK
First, the dowel will be heated to soften the glue and the glue inside of the attempted repair after the last attempt to reset the dowel. This stuff can go easy or hard and it is always hard to repair, a repair. Fortunately I have had enough of these kick my butt and have no fear. It will be ugly before it is pretty again. So let's go!
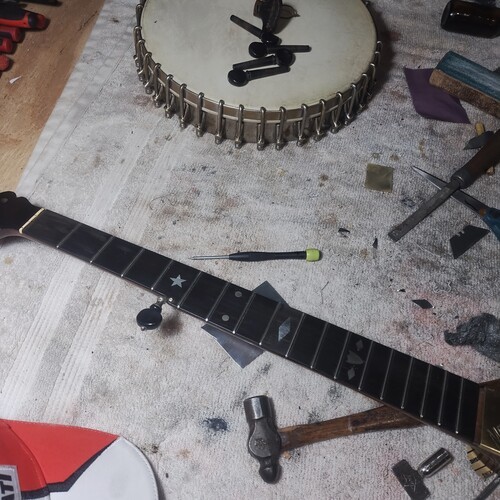
New aluminum inlay installed.
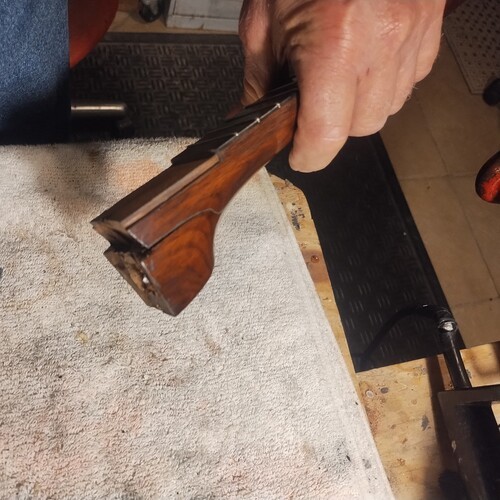
Now to remove the broken side piece.
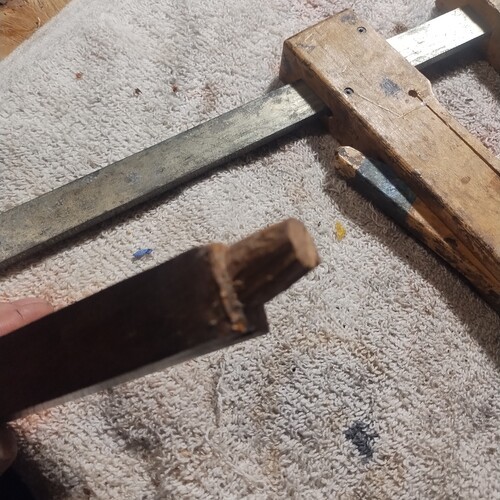
Dowel tenon made at an angle and at bottom of dowel,
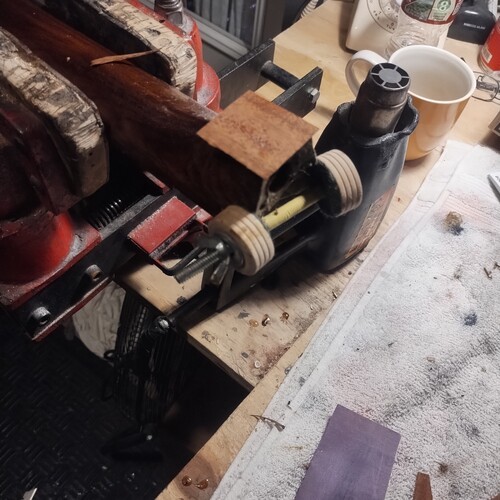
New heel cap after side piece cure.
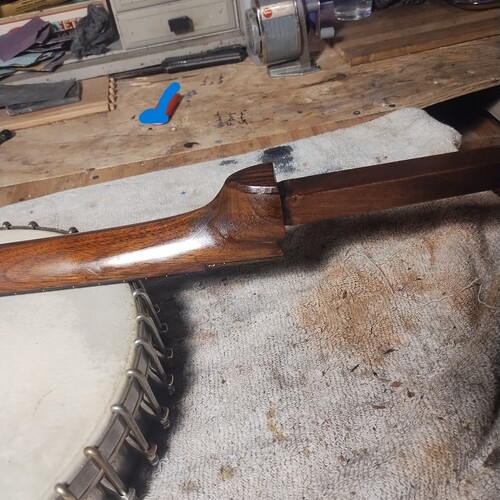
After sanding, clear coat. Repaired areas shown.
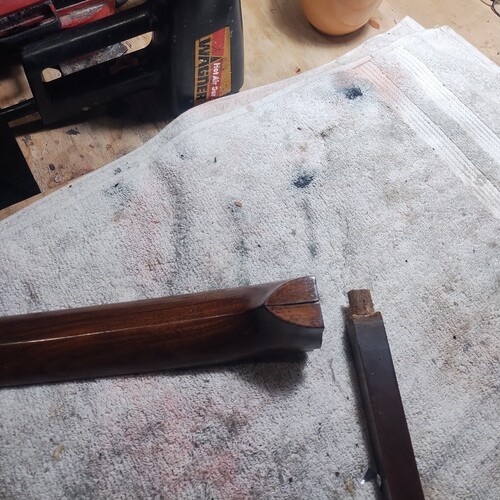
Short tenon on dowel , heel split shown.
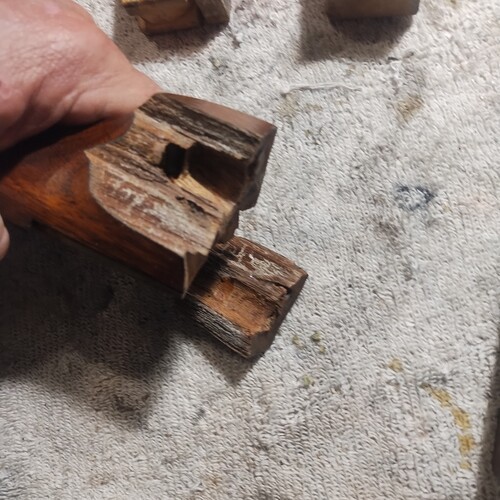
Akk of this will be cleaned of old glue
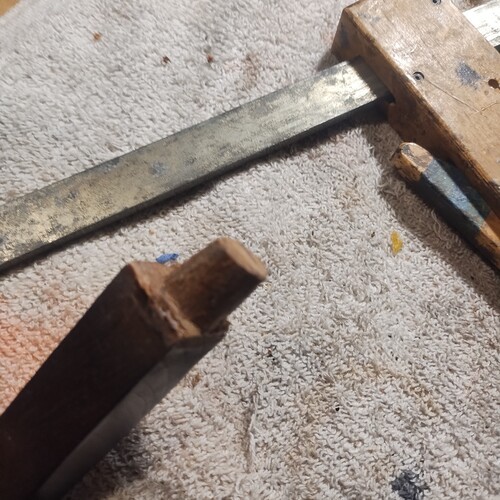
Many ways I have seen to make it have the right elevation, this one is new!
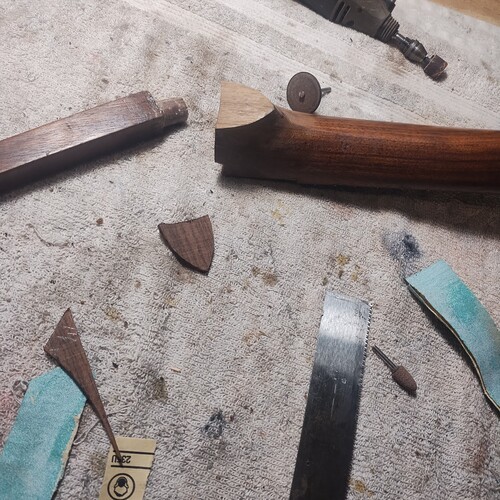
New 3/16 Rosewood heel cap for strength.
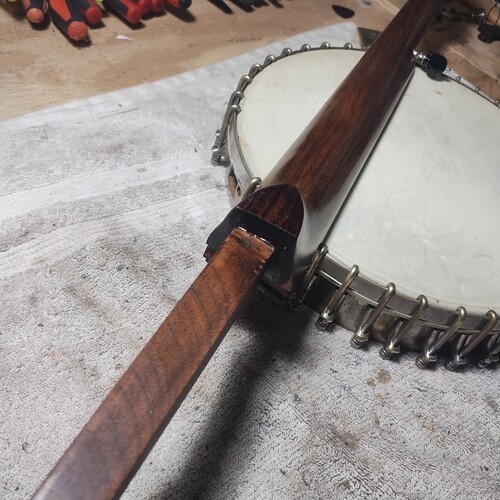
Now for some more clear coats.
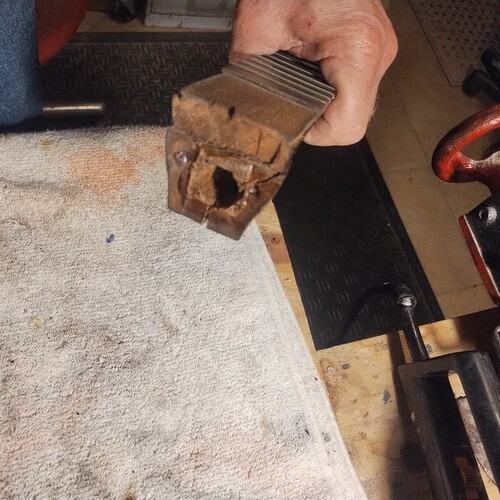
Factory handwork and old repair glue, yuck. I will fix all of that.
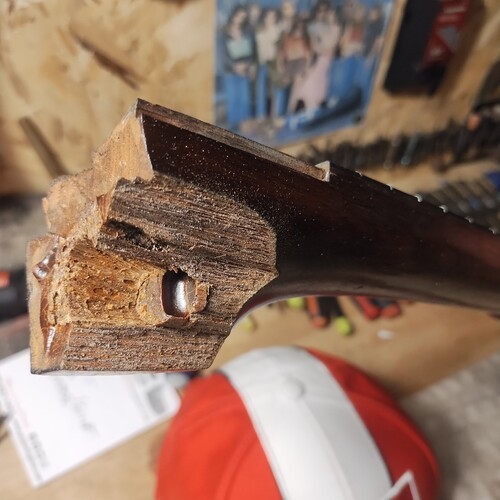
Old hide glue in pocket can be seen.
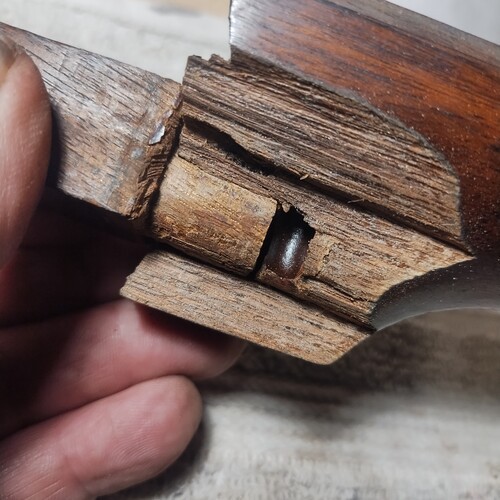
A rare glimpse of what we can never see, the glue pocket.
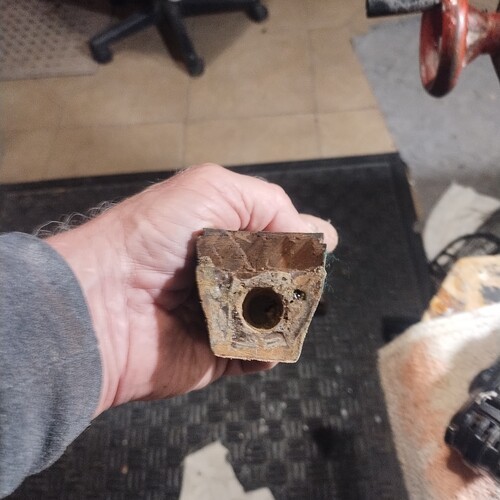
Starting on this area, it will be filled, contoured, etc.
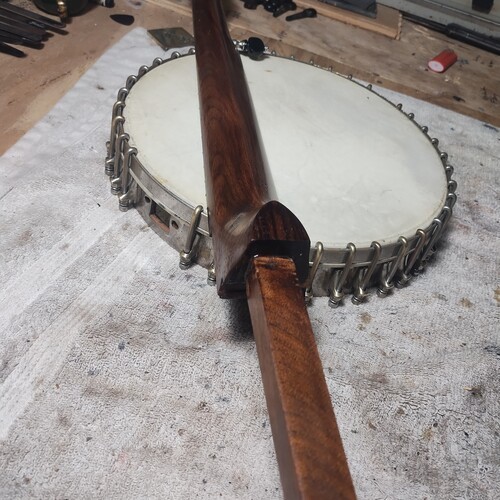
ASSEMBLY
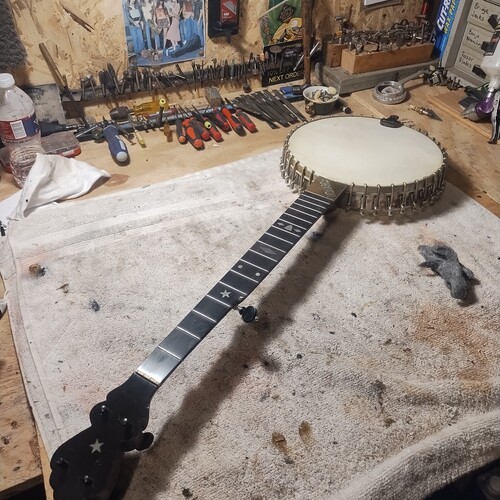
Ready to string with Aquila Classics
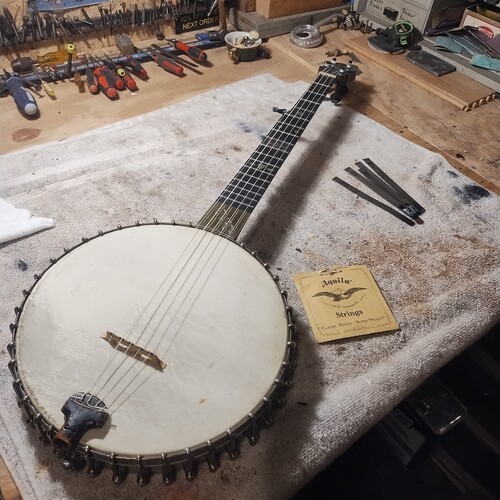
Nut/Bridge slots widened for Nylgut
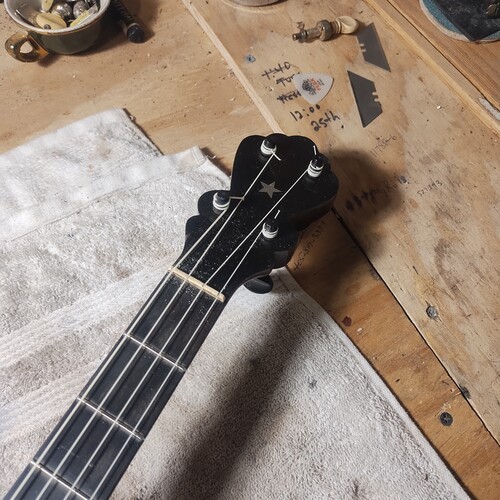

Nylgut, or, synthetic gut.
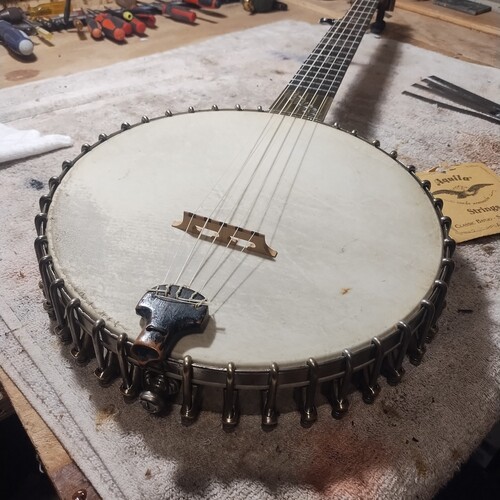
Plenty of bridge height with new neck angle.
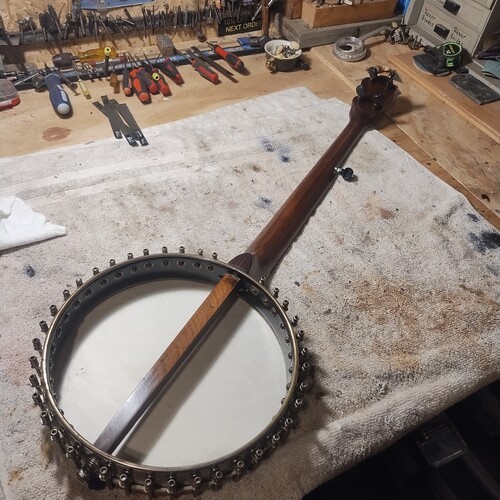
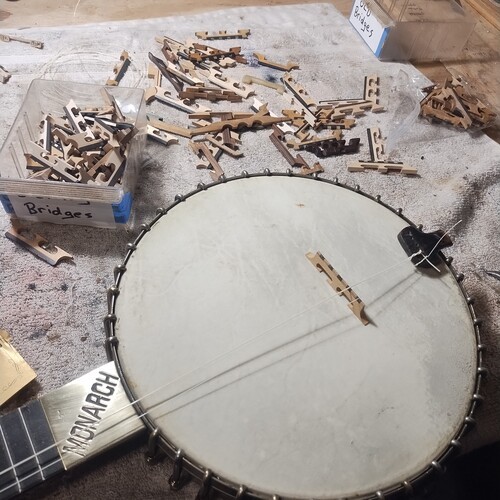
NOS Weymann bridge, period from that era.
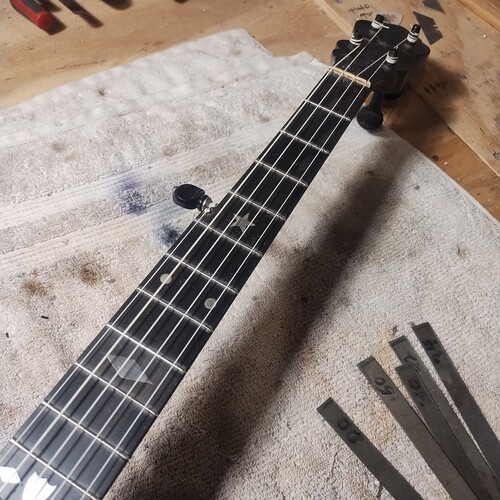
New inlay is a close match.
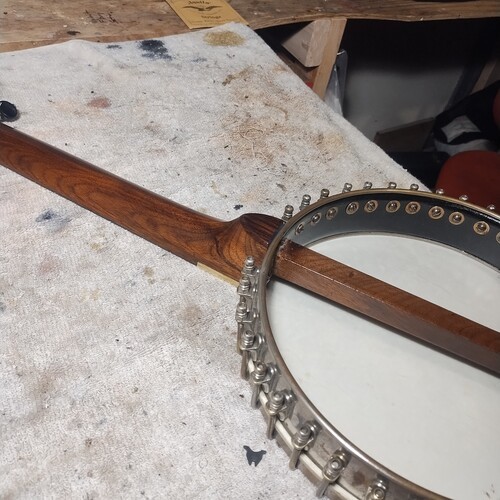
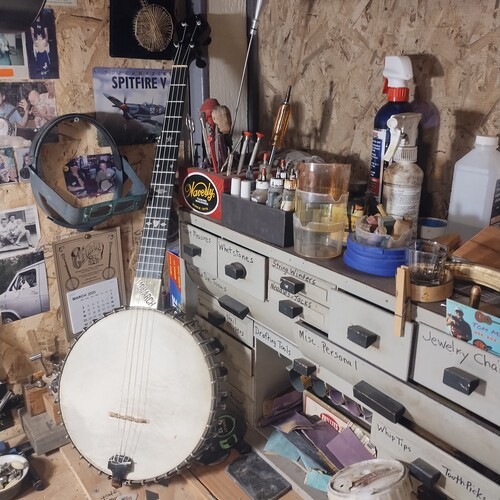
Plays out nicely, with a clear and focused tone.
Violin pegs are tricky but do hold tune.
Plenty of volume
Thanks for looking and sharing. VM
Violin pegs are tricky but do hold tune.
Plenty of volume
Thanks for looking and sharing. VM